Australian workplaces report over 300 serious injuries from electrical accidents annually, emphasising why proper electrical safety measures are important.
Test and tag colours create a simple visual system that helps organisations monitor their electrical equipment testing schedules.
The colour-coding system has become mandatory for Australian industries of all sizes. It lets people quickly check when equipment was last tested and identify upcoming inspection dates.
The Australian test and tag system assigns specific colours to different testing periods throughout the year. Safety officers, electrical contractors, and business owners must understand these colour codes to comply with Australian Standards AS/NZS 3760.
This article will cover the complete test and tag colour system, its real-world applications in different industries, and the best ways to implement it in 2025.
Understanding the Australian Test and Tag Colour System
Australia adopted a unified test and tag colour system in 2024. This system now operates throughout VIC, WA, NSW, SA, and QLD in accordance with the AS/NZS 3760 standard. The standardisation creates two different scenarios to implement test and tag colours.
Construction, demolition, and mining industries must follow specific colour codes based on AS/NZS 3012 guidelines. These sectors need to use the RGBY (Red, Green, Blue, Yellow) system that assigns different colours to each quarter of the year:
- Red Tags: December, January, February
- Green Tags: March, April, May
- Blue Tags: June, July, August
- Yellow Tags: September, October, November
Other industries have more flexibility with their test tag colours. While no specific colour schemes are legally required, companies can create their own colour coding system. Many businesses use red, green, blue, yellow, orange, white, black, and burgundy tags.
Companies operating in multiple states can maintain consistent testing schedules thanks to these optimised compliance requirements.
The best practice suggests conducting tests right at the start of each colour change period. This approach will give a full three-month validity period for the tag. Items tested close to a colour period’s end might need retesting once the new tag colour becomes active.
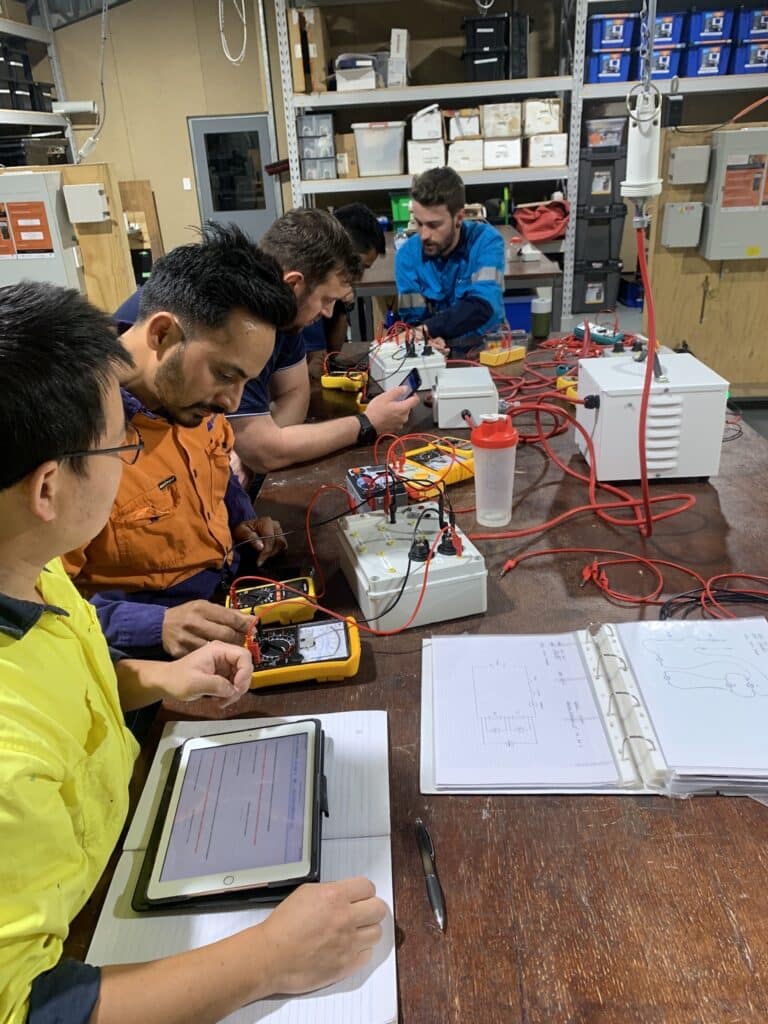
Practical Application of Test Tag Colours
A successful test and tag colour system depends on proper documentation and consistent procedures. Your organisation needs a clear process that defines the colour coding system with specific colours for each testing period and date.
The best time to conduct testing is at the start of each colour change period. This practice will give tags maximum validity since items tested near a period’s end might need immediate retesting when new colours take effect.
These best practices lead to successful implementation:
- Complete records of all test and tag activities
- The same standards at all sites and teams
- Staff training on the colour coding system
- Compliance requirement checks
- Proper documentation methods
Organisations outside construction have the freedom to choose colours, but they should assign different test tag colours for various re-testing periods and rotate them systematically. This system helps identify appliances that need testing quickly.
Documentation Requirements are vital to applying the system properly. Your organisation’s records must track the colour rotation schedule, testing dates, and equipment status. These records prove compliance and reveal patterns or systemic problems that need attention.
The core team members who handle the test and tag process need proper training to protect system integrity. They should understand the colour coding system and recognise how consistency and compliance matter in their daily work.
Implementing RGBY System for Construction and Mining
The RGBY (Red, Green, Blue, Yellow) system is the lifeblood of electrical safety compliance in construction and mining environments. Australian guidelines AS/NZS 3012 require these industries to conduct testing every three months. Specific colours designate testing periods throughout the year.
Essential Equipment Requirements Construction and mining sites must regularly test:
- Power tools and portable electrical equipment
- Extension cords and power cables
- Residual current devices (RCDs)
- Portable generators and lighting systems
- Communication devices and control panels
Testing and tagging duties can only be performed by staff members competent by their employer. Their competency stems from a mix of knowledge, skills, training and qualifications relevant to the task.
Testing should start at the beginning of each colour-coded period to maintain optimal compliance. This timing will give equipment tags maximum validity and maintain consistent safety standards. Equipment tested late in a colour period might need immediate retesting at the start of the new quarter.
Proper documentation is crucial to the system’s success. Each piece of equipment needs a durable tag after inspection that shows both the test date and next scheduled inspection date. This approach maintains safety standards in these high-risk work environments and ensures compliance with Australian regulations.
Non-Construction Industry Colour Guidelines
Australian standards offer more flexibility to industries beyond construction and mining when implementing test and tag colour systems. These sectors don’t need to follow the RGBY system but must keep consistent records and testing schedules.
Medical facilities use specific socket outlet colours that mean different things:
- White for normal supply
- Red for essential supply
- Blue for UPS backup supply
- Beige for cleaners’ outlets
Businesses can create their own colour rotation system based on how often they test. This flexibility lets them align their test and tag colours with their workplace’s needs while following AS/NZS 3760 standards.
Documentation Requirements Organisations using a custom colour coding system need complete records that show:
- Testing schedules and frequencies
- Colour rotation systems
- Equipment inventories
- Testing results and compliance certificates
Success depends on staying consistent and communicating clearly. The chosen colour scheme should be well-documented and shared with all departments, regardless of whether testing happens quarterly, semi-annually, or yearly.
Healthcare facilities face extra requirements to protect patients. Socket outlets must show power availability indicators and RCD protection status markings. These special requirements show how different industries can adapt their test and tag colour systems to meet safety needs while following Australian standards.
Maintaining Electrical Safety Through Proper Test and Tag Practises
Test and tag colour systems are a vital part of Australia’s workplace safety framework. This standardised approach helps companies track their testing schedules and stay compliant with AS/NZS 3760 standards in various industries.
Construction and mining sectors benefit from the mandatory RGBY system, while other industries can create custom colour schemes that match their needs. Medical facilities show how specific requirements can fit into the broader test and tag framework.
Your system will work well if you focus on these essential elements:
- Keeping consistent documents and records
- Training staff regularly with updates
- Making colour coding systems clear to everyone
- Following testing schedules strictly
- Taking care of equipment properly
Safety officers and business owners can boost their electrical safety knowledge through Get Skilled Training’s Test and Tag Course, available across Australia. This professional development helps the core team stay up to date with Australian standards and best practices.
The test and tag colour system keeps adapting to new workplace needs while serving its main purpose – protecting workers and equipment through organised electrical safety management. Companies can create safer workplaces that meet both regulations and practical safety needs by implementing the system properly and updating it regularly.